Realizing a Recycling-Oriented Society
Basic policy
The AMADA Group is committed to resource conservation and recycling in all processes of its business activities and thoroughly pursues the reduction of environmental load. We also assess the impact of our operations on the natural environment and are committed to the effective use of water resources.
Effectively using resources
The AMADA Group promotes the effective use of limited resources to help bring about a recycling-oriented society. At our domestic production bases, we place importance on the transition to a sustainable society and are making efforts to make them zero-emission factories and clean factories.
Zero-emission factories
At our manufacturing bases, we are taking waste reduction efforts in three steps: exit control, entrance control, and source control.
A factory is designated as a zero-emission factory if its ratio of final landfill waste to total emissions (zero emission rate) is less than 1%, and if this ratio has been maintained for at least one year. The AMADA Group achieved zero emissions at six manufacturing bases in Japan: Isehara Works (AMADA TOOL), Fujinomiya Works, Toki Works, Noda Works, Fukushima Plant, and Isehara Suzukawa Works. In fiscal 2019, the AMADA Group achieved a Groupwide zero emission rate of less than 1% (0.81%), and has made further efforts since.
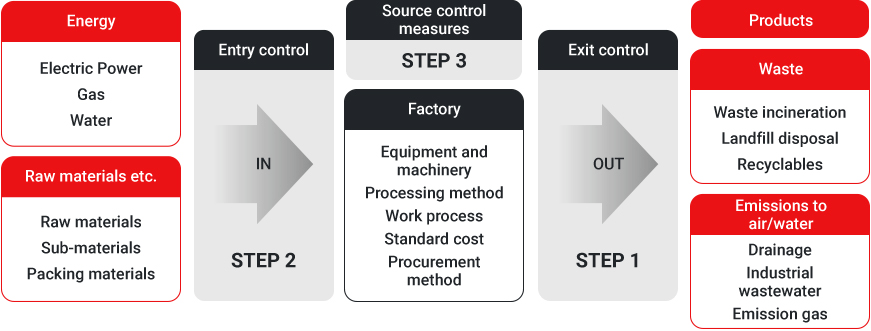
Effectively using resources and reducing waste during manufacturing
Recycling cutting fluids contributes to waste disposal reduction (Toki Works)
The water-soluble cutting fluids used previously caused odor problems and sludge buildup in tanks, making it necessary to change the cutting fluids once every six months. By switching to alkaline ionized water, we have been able to prevent the decay of cutting fluids, as well as the particularly unpleasant odors characteristic of processing stations. This also prevents the adherence of dirt to machine interiors, lengthens the time between cutting fluid changes, and results in a substantial reduction of waste fluid emission.
Waste disposal reduction through new material handling systems and resin pallets (Toki Works)
We have stopped using wooden pallets for delivery of castings, and now use reusable resin pallets and palletainers (metal cage-style containers).
All pallets and palletainers are numbered, and managed with oversight of the persons in charge of material reception attending each delivery.
We have also developed an assembly and transport material handling system that can be used repeatedly for sheet metal delivery. This has enabled us to achieve our packaging material goals of zero wooden pallets and zero plastic sheets.
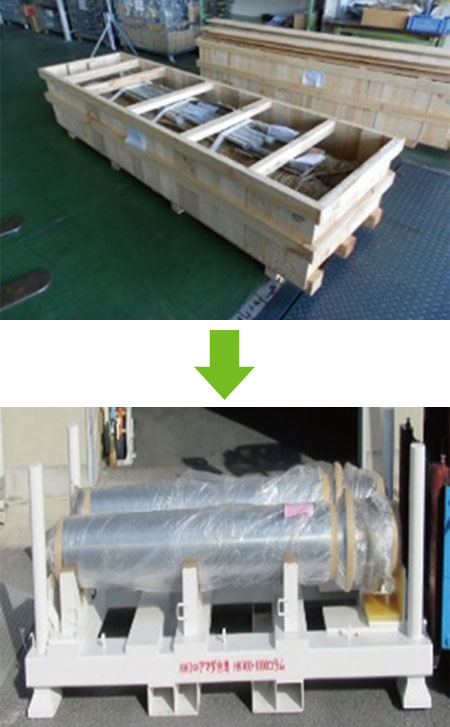
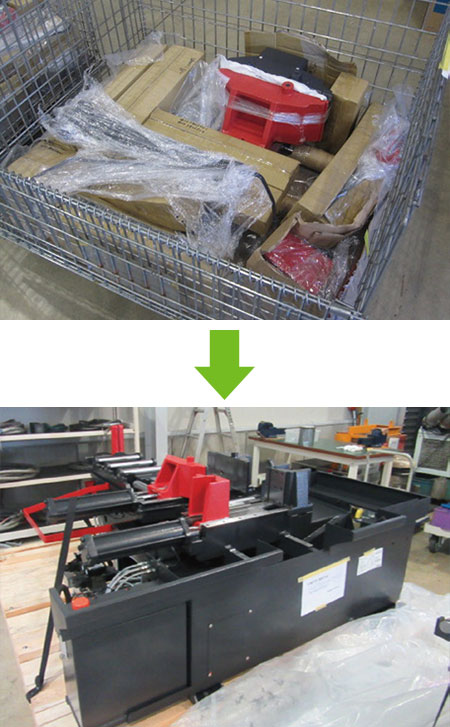
Effectively utilizing scrap wood (Fukushima Plant)
Scrap wood from ASR (cycle loader: a material stack and supply system) are utilized for IT-TSU (tooling exchanger) frames, automated material storage system (MARS) pallets, etc., resulting in reduced waste emissions and less purchase of new materials.
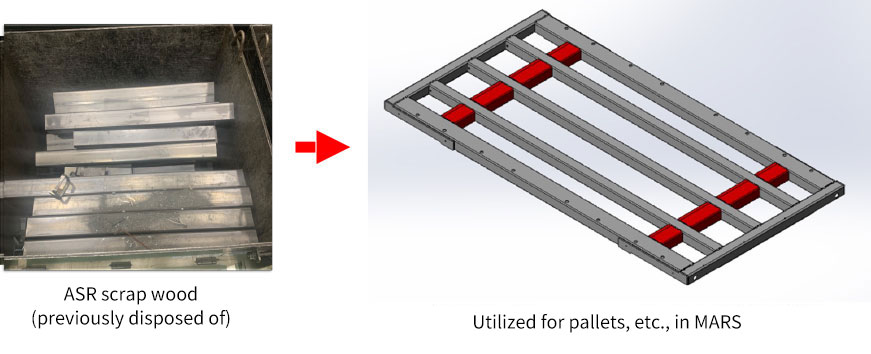
Effectively using resources and reducing waste during packaging and transportation
Ongoing efforts are being made to reduce waste from packaging materials used in transfers to suppliers and in the delivery of products.
Conventionally, plastic air caps, oilpaper, cardboard, and other packing materials were used and discarded after unpacking, but we have created special packing materials tailored to each product, which are reused multiple times to reduce the amount of packing material waste. The use of special packing materials reduces packing and unpacking time, as well as transportation efficiency due to smaller packages.
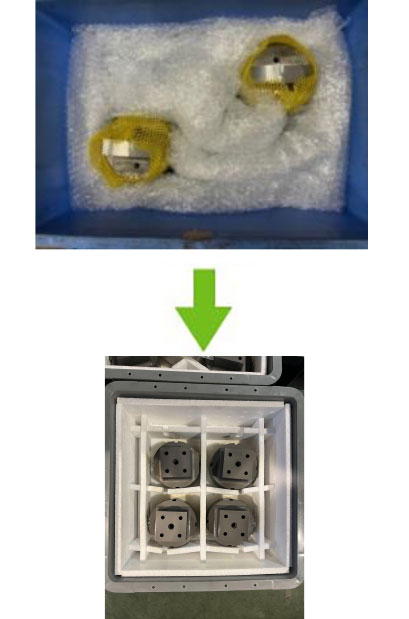
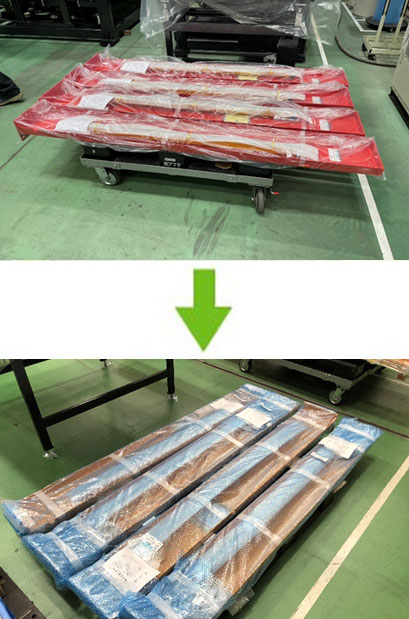
Effectively using resources and reducing waste during sales
At the product sales stage, in addition to sales activities for AMADA Eco-Products, we are also working to be environmentally mindful in our exhibitions. Decorative components used in public exhibitions have been switched to system components that are reusable a number of times, and parts that are difficult to reuse are processed for recycling.
In addition, decorative components used for in-house exhibitions are transported to the Isehara Works for reuse in an effort to reduce waste.
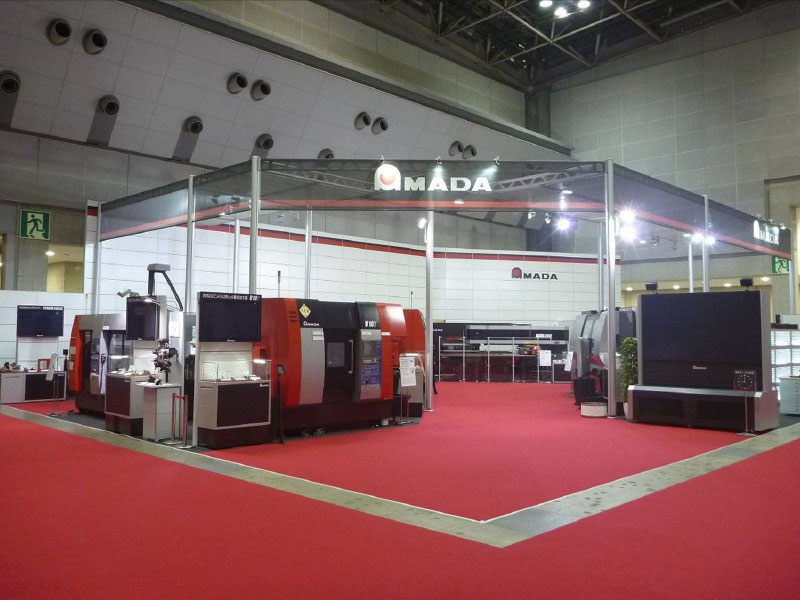
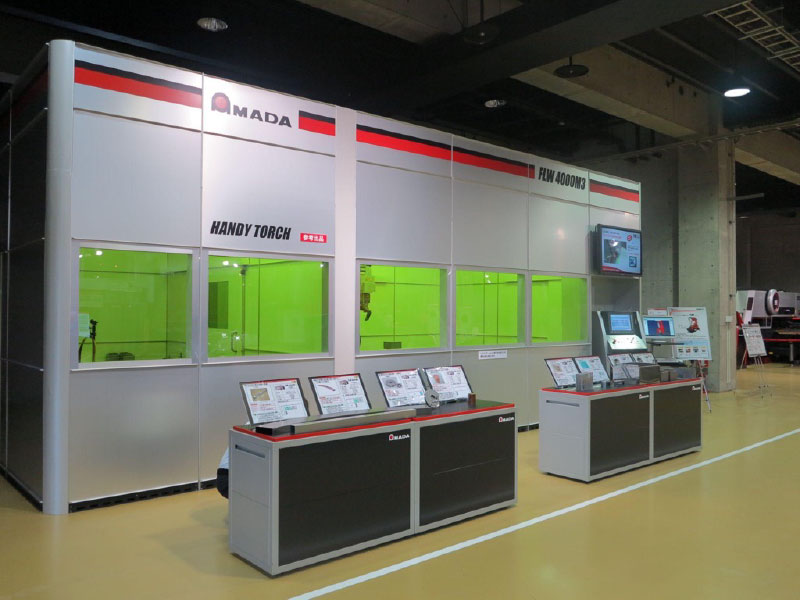
Collection and recycling of used products
The AMADA Group certifies companies to which it outsources disposal operations based on the Group’s selection criteria to ensure that products are properly disposed of when they reach the end of their useful life. From fiscal 2008 to now, we have certified five sites across two partner companies, where recycling plants have secured compliance with various laws and regulations and product disposal is done appropriately.
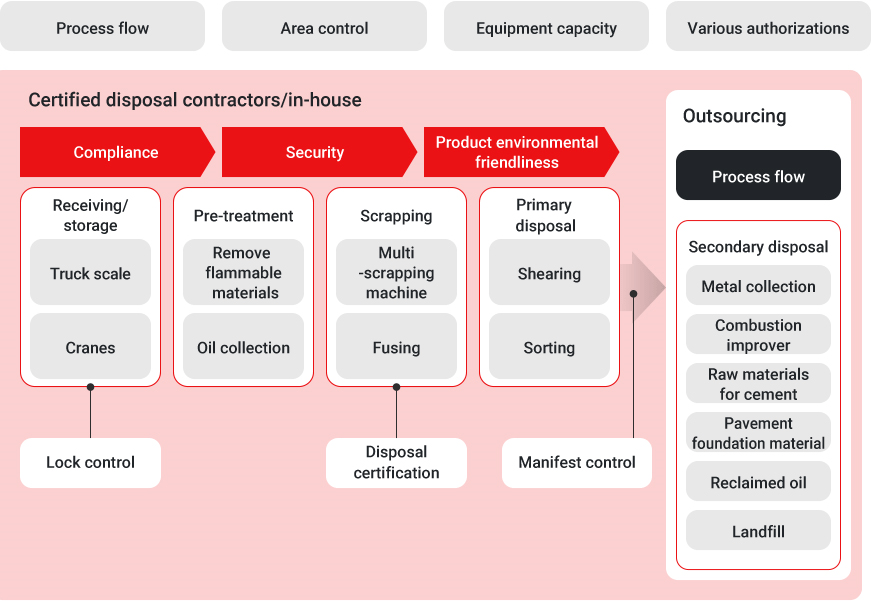
Conserving and effectively using water resources
Of our AMADA Group Environmental Policies, “3. Efforts to live in harmony with nature” states that we will maintain an awareness of the effects of business activities on the natural environment and make efforts to live in harmony with nature by using water resources effectively and protecting biodiversity and ecosystems. With the aim of sustainable use and conservation of precious water resources, we have set a goal of reducing the Group’s overall water consumption by 10% by fiscal 2030 (compared to fiscal 2019) by conducting water risk assessment and formulating an action plan.
Leveraging global tools to assess water risks
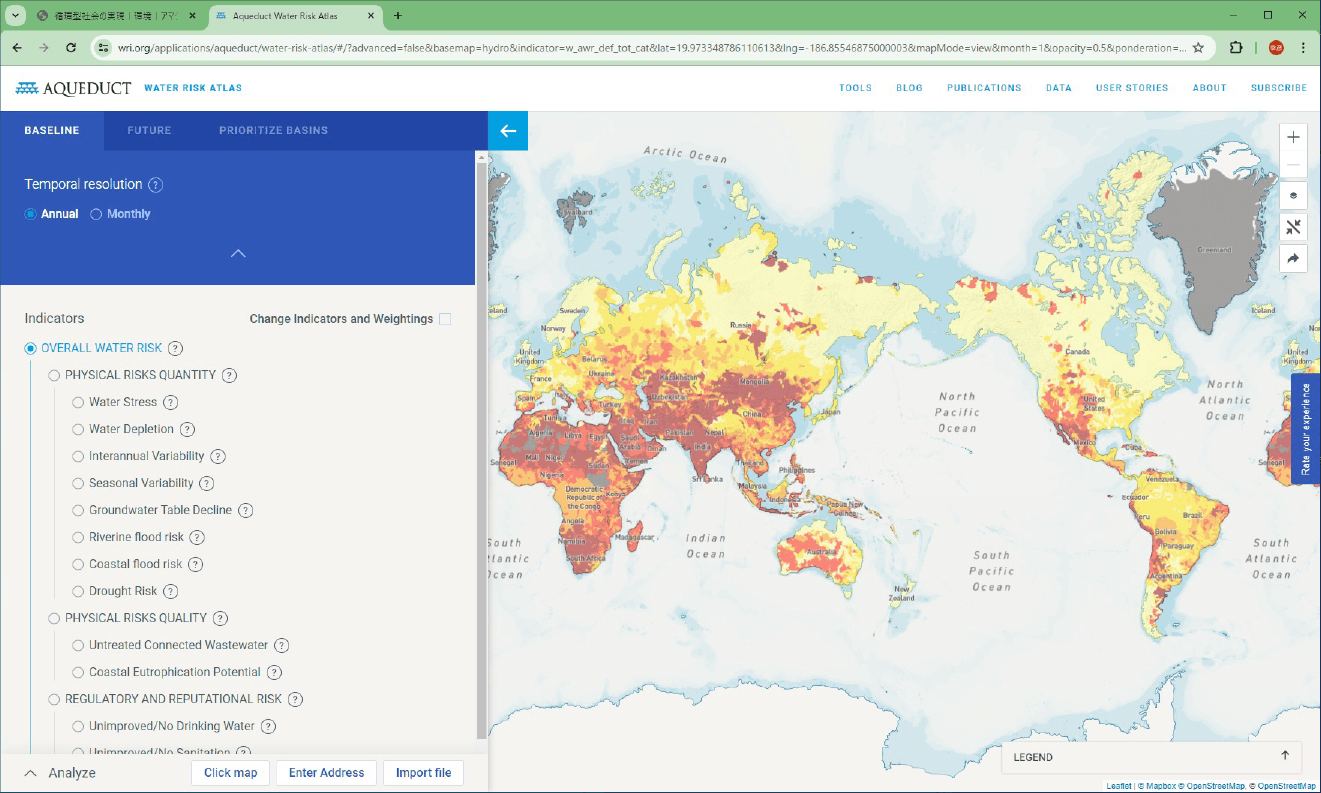
In September 2023, we used the Aqueduct tool by the World Resources Institute to assess water risks for the AMADA Group. Compared to the previous assessment, the September 2023 assessment was expanded to include all bases, not just manufacturing bases. In this assessment, water risks regarding all 66 bases in Japan and overseas have been identified and analyzed.
The overall water risk assessment results showed that the physical risks (quantity) were high risk. We found that 16 bases (North America 6, Europe 3, Asia 6, Others 1) had level 4 water stress risk*1, the highest level for water stress risk and presenting one of the highest risks overall. The total amount of water intake in these areas of high water stress risk (49,815 m3) for the AMADA Group accounts for 37.4% of the total water intake for all bases outside Japan (133,361 m3).*2
- Note:1. Water stress risk is calculated as the level of water demand relative to the amount of water resources and indicates the degree of water scarcity in a region.
- 2. Water withdrawals and water withdrawal ratios are based on FY2023 data.
12 assessable indicators with Aqueduct
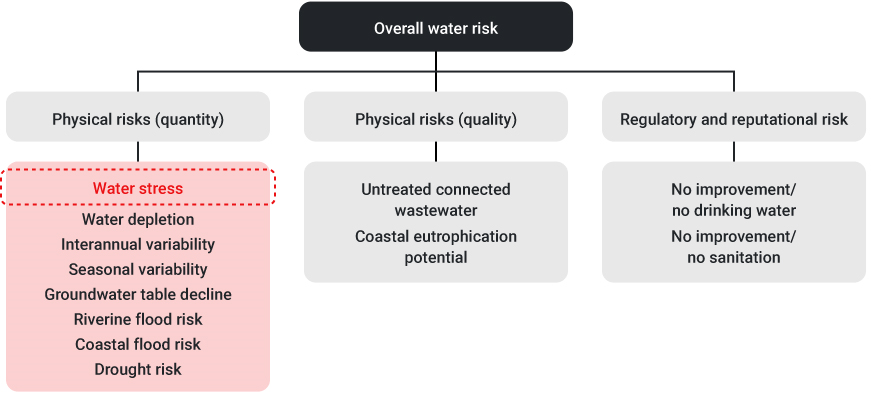
- Created by AMADA based on the Aqueduct Water Risk Atlas website
Reducing water consumption
Outside Japan, we reduced water consumption through more efficient water use, including irrigation management and improvement on some facilities (reduction effect of approximately 9,000 m3). In Japan, the reduction in usage of water sprinklers at the head office and other seasonal and careful usage on the premises contributed greatly to reduction (reduction effect of approximately 22,000 m3). As a result, by the end of fiscal 2024, we had already exceeded our reduction target for 2030 (10% reduction versus 2019 levels). For our track record in this area, please see the page linked below.
Environmental Targets and Plans