Manufacturing
Employee-friendly manufacturing system for producing high-quality products
To ensure the stable operation of machines at its customers’ plants, the AMADA Group is rigorous in its quality control more than anything else. So that each worker is equipped with the skills for advanced manufacturing, we maintain the necessary regulations and provide training through the “Quality Dojo” quality training center. With 24 manufacturing bases located both domestically and internationally, we aim to deliver promptly to customers in all regions. From a business continuity plan (BCP) perspective, we strive to produce locally at each region’s bases.
In our own manufacturing, we utilize IoT for efficient, human-friendly production by providing digital technology support at the level of the factory as a whole and to each individual worker. Furthermore, we are working to reduce CO2 emissions in manufacturing, seeking a 75% reduction (vs. fiscal 2013 levels) by 2030 at all Group business sites and plants.
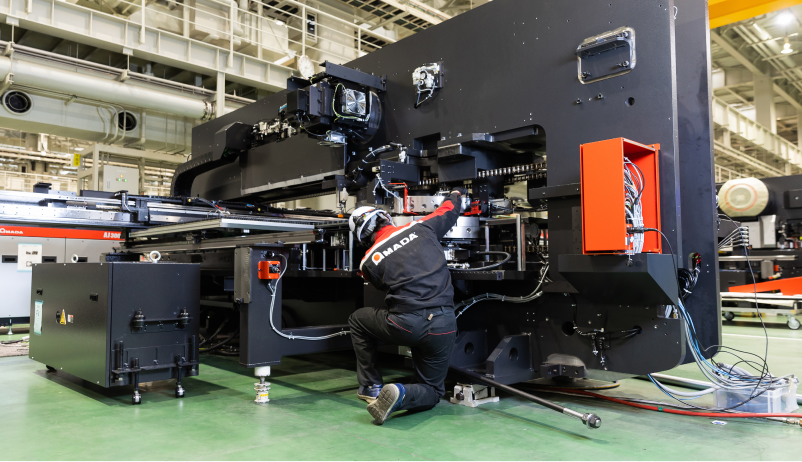
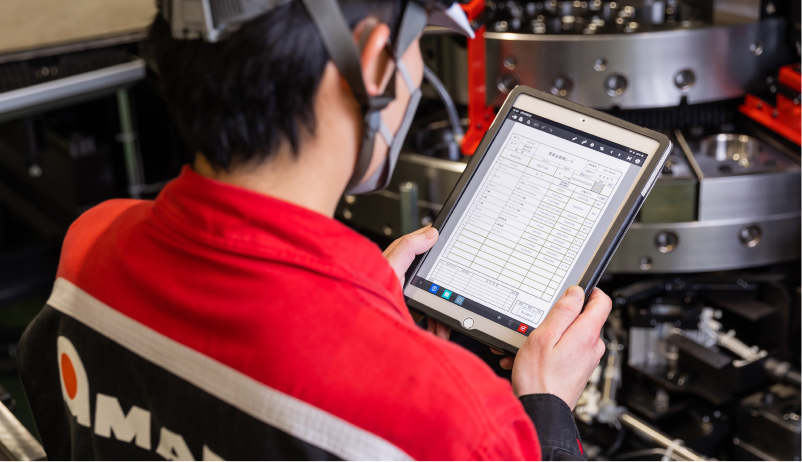
Quality management centered on the Fujinomiya and Toki Facilities
Major modules found in sheet metal fabrication machines are produced at the Fujinomiya and Toki facilities under rigorous quality control, after which they are delivered to the Group’s overseas production bases.
We strive to maintain and improve global product quality, with the Fujinomiya and Toki facilities serving as the mother factories for sheet metal machine manufacturing.
Furthermore, by promoting DX and strengthening collaboration among offices and plants, we are strengthening our flexibility and adaptability to change.
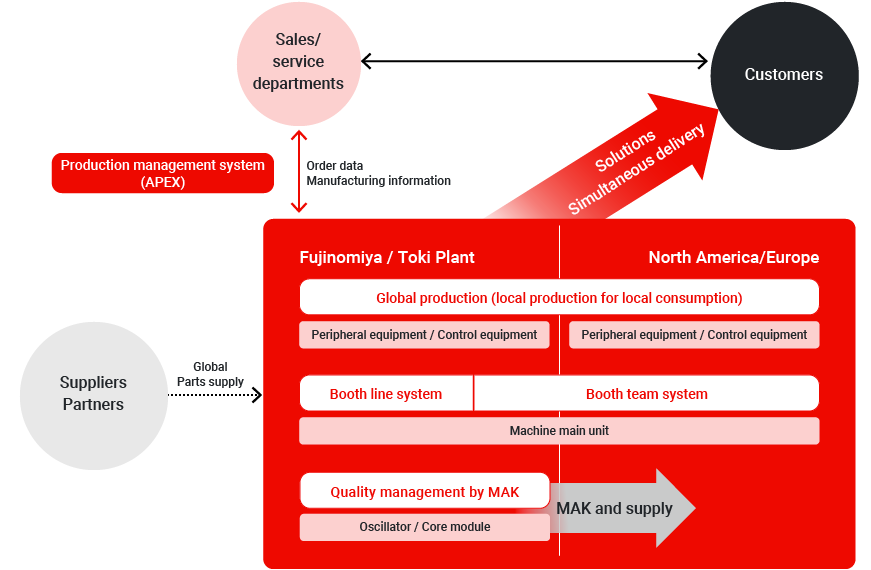
MAK quality control and employee-friendly manufacturing
The AMADA Group has adopted the MAK approach to increase productivity while ensuring quality. This refers to “M (module),” where functionality and performance are inspected using simulators; “A (assembly),” where assembly precision is checked with inspection equipment; and “K (kit),” where multiple parts are collected and supplied according to work procedures.
For modules, which provide the core functionality of processing machines, we ensure that workers can perform their tasks in the optimal posture. This is done by providing a dedicated worktable that is movable to a height suited to the operator and establishing appropriate work procedures. Since this keeps workers from being forced into unreasonable postures, standard work can be maintained at a high level regardless of worker physique, thereby ensuring consistent quality.
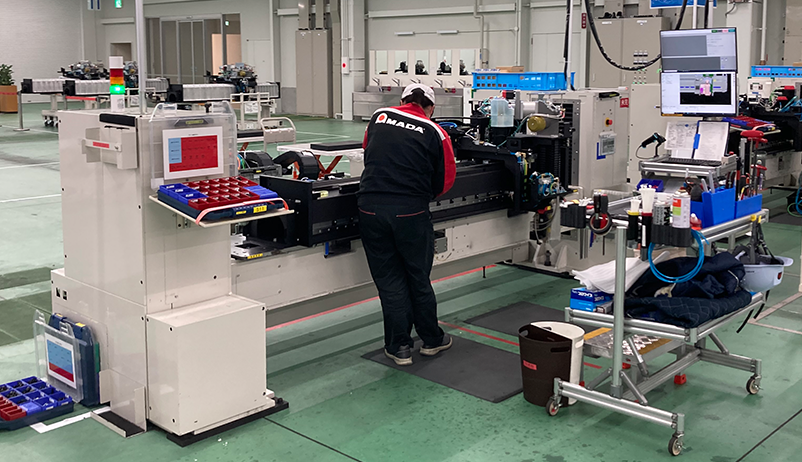
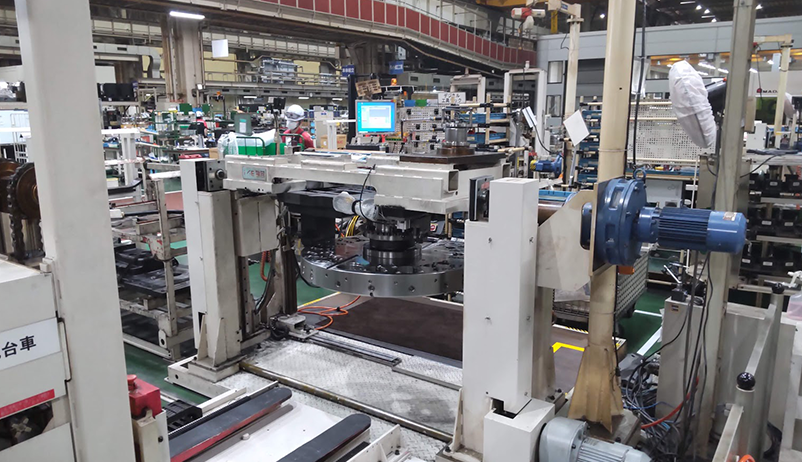
Global production
As part of our global production efforts, laser oscillators and core modules, which are key elements for ensuring quality, are supplied from our core plants in Japan to maintain uniform quality throughout the world. At the same time, each production base is committed to local production for local consumption, and peripheral equipment and control systems are locally designed to meet the needs and procurement environment of each region. We also engage in aggressive global procurement to achieve competitive manufacturing costs.
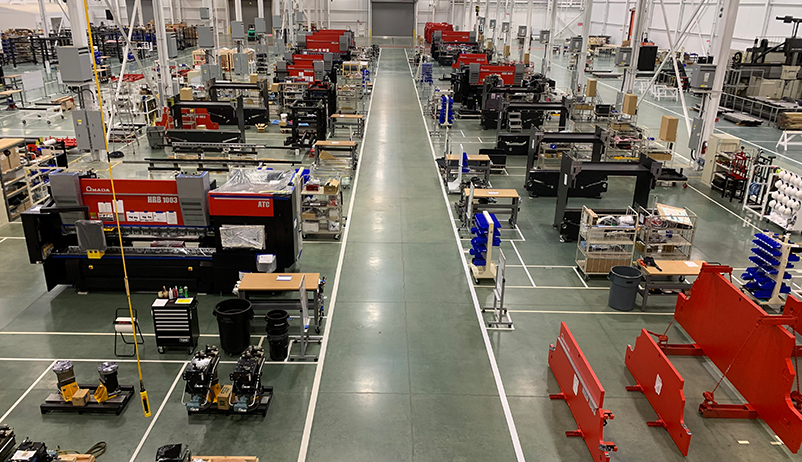
Booth Line System
The assembly process is conducted in booth stalls, which are separated by white lines for each unit. To accommodate the characteristics of the product models and customer needs, we have adopted two production methods: the "Booth line system" and the "Booth team system." The "Booth line system" is a mass production method where workers repeat the same assembly process, resulting in improved production efficiency and shortened lead times. The "Booth team system" is suitable for small-lot production of various models, where dedicated workers assemble the products in teams, ensuring high-quality products.
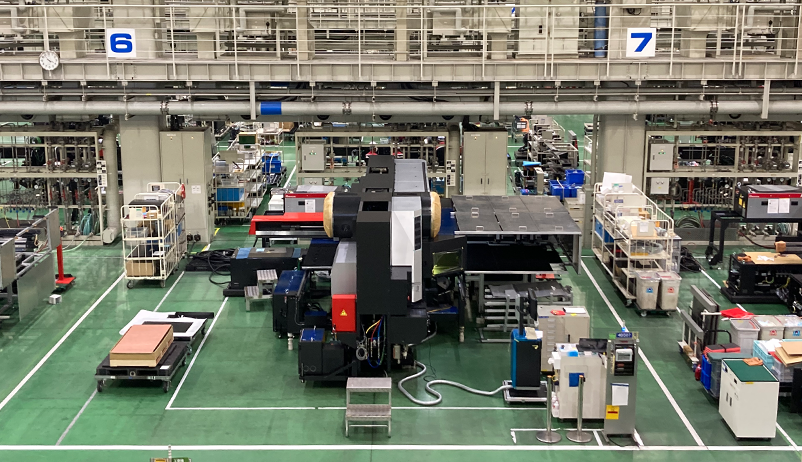
Production system: AMADA Production Environment Transformation (APEX)
AMADA’s unique production system integrates with sales, development, and procurement information, enabling the optimization of production planning and scheduling, inventory status-based order management, and the immediate detection of process impediments through visualization of work progress. In addition, we have established an environment of instantaneous information sharing with our subcontractors via our portal site, making available up-to-the-minute information on delivery dates and parts reserves.
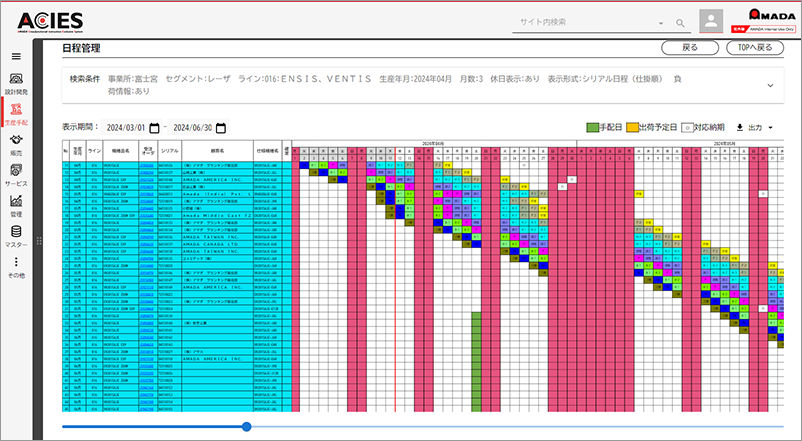