Digital Transformation
The manufacturing environment is currently undergoing rapid change. In particular, there is a need to work toward a decarbonized society, address labor and skilled worker shortages, and adapt to high-mix, low-volume production. These challenges are shared by AMADA's customers as well as AMADA itself, the manufacturer. As a solution, we are promoting digital transformation both internally and for our customers.
For digital transformation, customers use LIVLOTS, a manufacturing solution linking information from their manufacturing sites, offices, and program rooms, and V-factory, which lets them visualize their production status and provides IoT support to keep their operations up and running.
AMADA's internal digital transformation efforts fall into two main categories. One is sales and service. We take the experience and knowledge we have accumulated through our unique direct sales and direct service and apply them to data-driven sales and service, thereby simultaneously strengthening and streamlining our customer support activities.
The other is development and manufacturing. Through digital transformation, we are improving operational efficiency through digitization and data linkage of each department's operations, and strengthening ECM (Engineering Chain Management) and SCM (Supply Chain Management). Especially in SCM, we are strengthening relations with suppliers, having reflected on the delays in lead times for delivery to customers during the COVID-19 pandemic.
AMADA has long supported global manufacturing by repeatedly “creating” and “taking on challenges.” Leveraging digital transformation and AI technologies, the AMADA Group is currently gaining a new source of strength to “develop together with our customers.” The goal of these efforts is to optimize and streamline the complex production conditions facing our customers, and to grow alongside them.
Through the digital transformation of worldwide manufacturing, AMADA will continue to drive innovation and contribute to the realization of a sustainable industrial society.
In November 2024, AMADA CO., LTD was approved by the Ministry of Economy, Trade and Industry as a DX-certified operator under the Digital Transformation Certification System.
Digital Transformation of Customers
LIVLOTS, Digital Transformation Solution
This system achieves waste-free production by handling variable quantities of different types of products.
By connecting the customer's offices, program rooms, and manufacturing sites, LIVLOTS gathers the information required for production (workers, product information, and job details) and navigates top-priority jobs to specific worksites and individual processing machines.
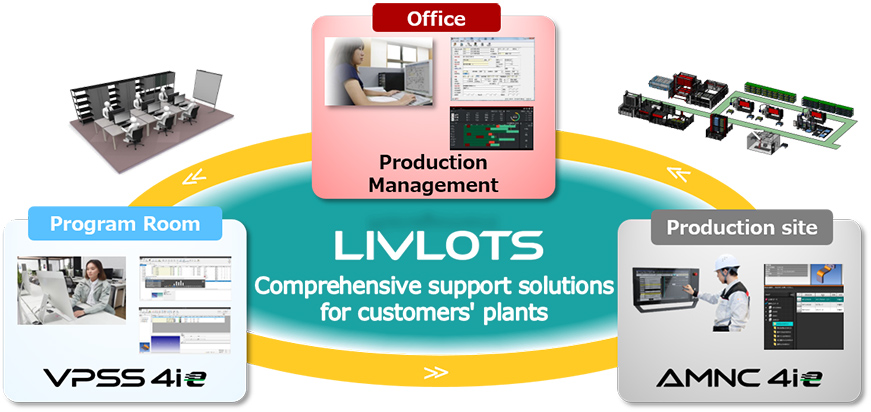
V-factory, Digital Transformation Operation Guarantee
A comprehensive effort to keep customers' manufacturing operations up and running, our digital transformation operation guarantee provides customers with support through three mechanisms.
- Preventive maintenance (IoT machine health check)
The operational status of each machine is constantly monitored for each customer through the IoT. The health of machines is maintained through constant remote diagnostics without having to shut them down. - Remote Digital Inspection
Periodic inspections of machines are arranged according to their condition at that time, utilizing vast amounts of data accumulated through IoT. - Real-time diagnostics
When problems occur that cannot be foreseen even with preventive maintenance or inspections, IoT support staff use machine operation data to identify the cause and assist in early recovery. A service engineer can also be dispatched, or emergency treatment performed by remote control.
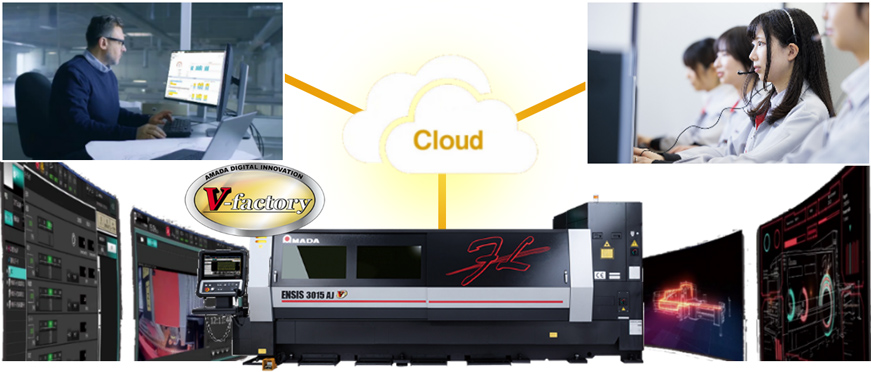
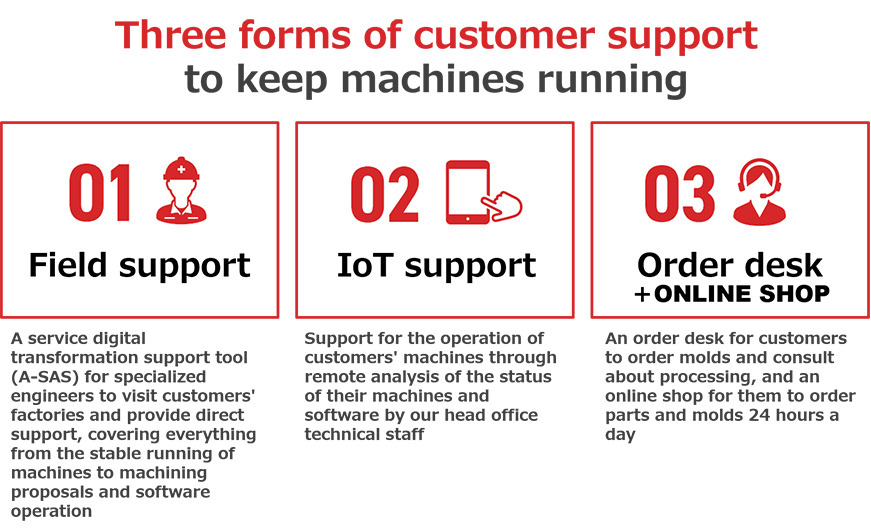
Digital Transformation within the Company
ADMS, Sales and Service
Amada will evolve its unique “direct sales and direct service” business process into “data-based digital sales and service,” establishing a system to strengthen customer support and streamline sales activities.
By introducing an ADMS, we aim to create new business opportunities and solve social issues faced by the manufacturing industry through the analysis of marketing data. This will also enable us to provide superior products and services, accelerating our growth as we approach our centennial.
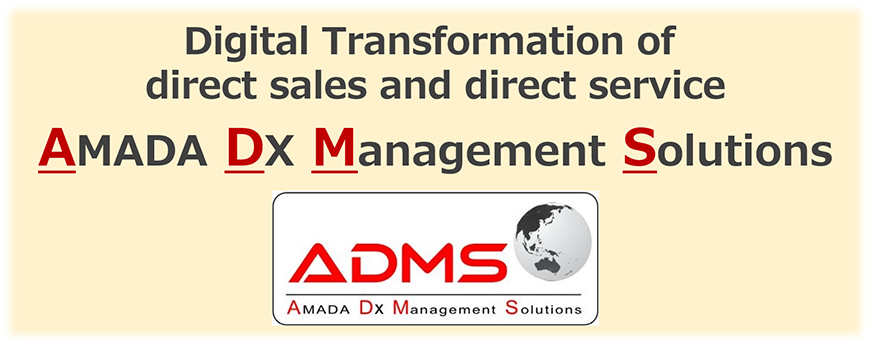
Utilizing a sales/service assistance system (A-SAS), customer proposal tool (A-Pro), and project acquisition automation (A-MAX) as growth acceleration engines, we will improve action efficiency, increase sales per employee, and make new employees immediately effective.
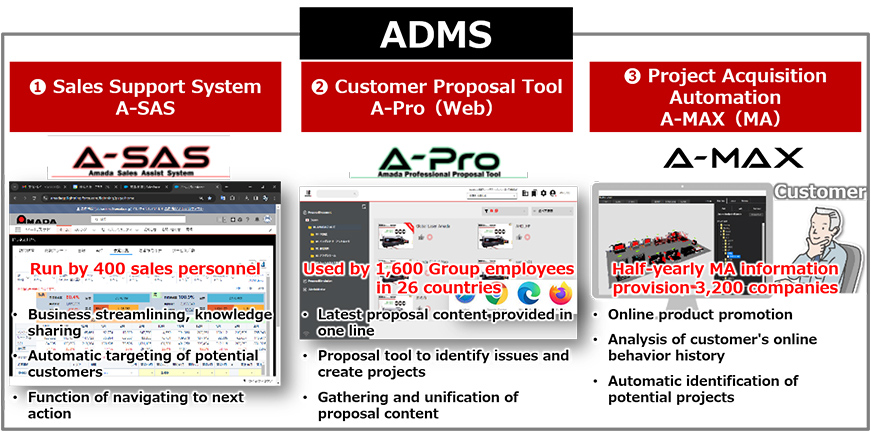
APEX, Development and Manufacturing
In recent years, increasingly sophisticated customer needs have led to diversification of product specifications. In response to these changes, and in addition to existing efforts, Fujinomiya Works, where development and manufacturing are co-located, has begun reform utilizing digital transformation along two axes: SCM (supply chain management) which links production information from sales through production planning, procurement, and manufacturing; and ECM (engineering chain management) which links technical information from development to manufacturing and services.
This reform is collectively referred to as APEX, an acronym for “AMADA Production Environment Transformation,” which we are taking to its peak.
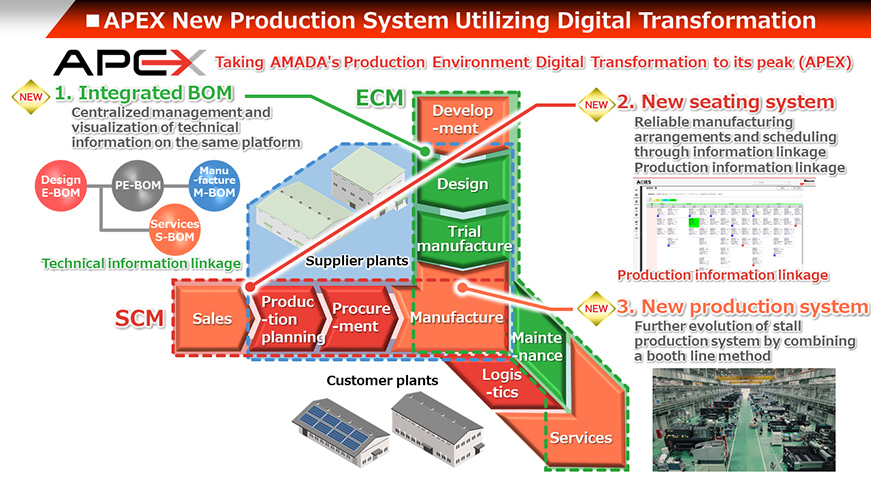
First, we have created new content to support this reform, an integrated BOM with design (E-BOM), manufacturing (M-BOM), and service (S-BOM) on the same platform.
Leveraging the advantages of our integrated manufacturing and sales system, Amada has strengthened linkage and updated the new seating system to be able to respond more flexibly to customer requests, such as when drawing up or changing production plans.
At our plant, we have further evolved our stall booth production system by concurrently using booth line production.
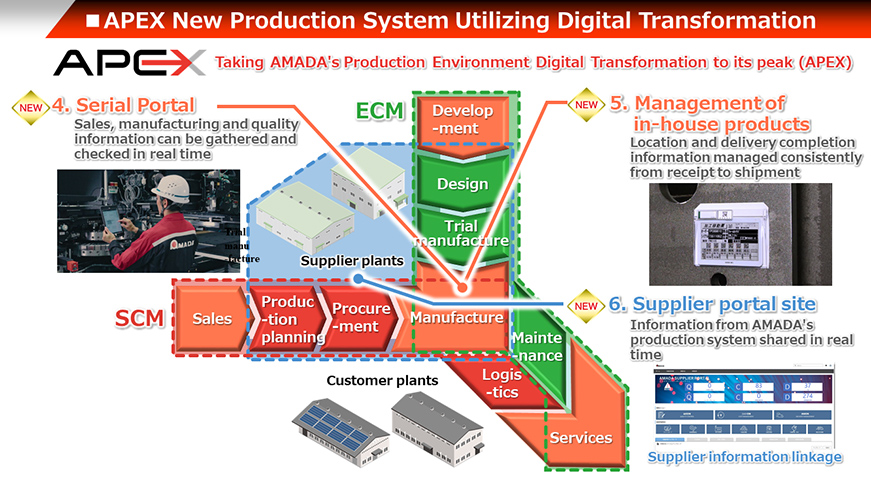
Regarding parts management, we aimed for a system that enables real-time management of information on the location and delivery completion of parts from receipt to shipment.
A serial portal allows on-site workers to check sales, manufacturing, and quality information for each machine serial at any time.
On the Supplier Portal site, real-time information is linked in both directions with suppliers in procurement activities, improving QCD in parts procurement and the efficiency of indirect operations.
Leveraging Generative AI
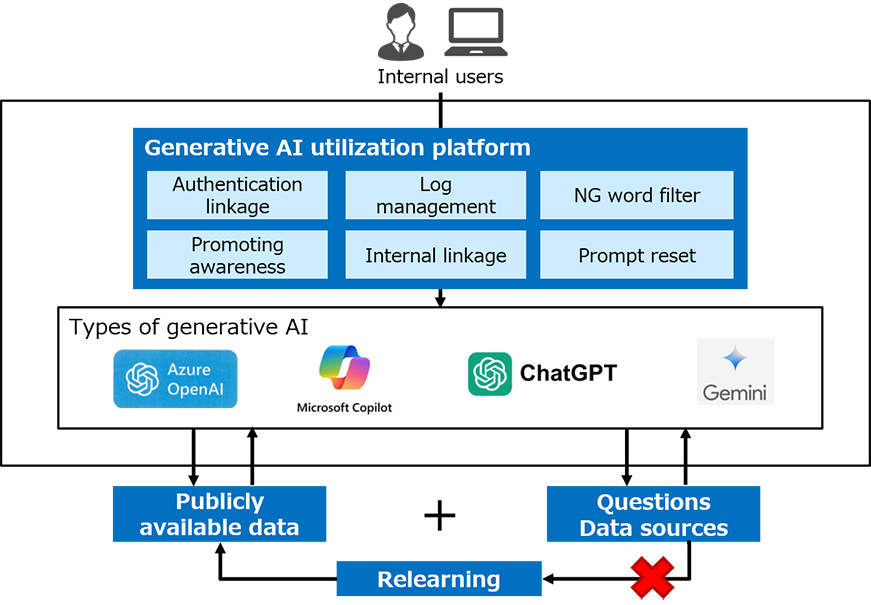
We have built a platform for using generative AI that can accommodate both patterns of using publicly available data (online) and using internal data only, and are operating them for internal operations. The use of internal data only is for purposes such as IT and CAD help desks, handling general affairs inquiries, and searching for quality-related data.
When using publicly available data, we do so in an environment that prevents the leakage of confidential information or infringement of copyrights. It is not used as training data for generative AI.