循環型社会の実現
基本的な考え方
アマダグループでは、事業活動のすべてのプロセスにおいて、省資源、リサイクルに取り組み、環境負荷の低減を徹底的に追求しています。また、事業活動に伴う自然環境への影響を把握し、水資源の有効活用にも取り組んでいます。
資源の有効活用
アマダグループは、限りある資源の有効利用を促進し、循環型社会に貢献します。国内生産拠点においては、持続可能な社会への転換を重要視しゼロエミッション工場の達成から、クリーン工場をめざした活動を推進しています。
ゼロエミッション工場
製造拠点では出口対策、入口対策、発生源対策の3ステップで廃棄物削減の取り組みを進めています。
全排出物の中で最終埋め立てされる廃棄物の比率(ゼロエミッション率)が1%を下回り、さらにその状態を1年以上継続した工場を「ゼロエミッション工場」と定めています。アマダグループ国内製造拠点の中で、伊勢原事業所(アマダツール)、富士宮事業所、土岐事業所、野田事業所、福島工場、伊勢原鈴川事業所の6拠点にてゼロエミッション工場を達成しました。アマダグループでは2019年度にグループ全体でのゼロエミッション率1%未満(0.81%)を達成。その後もさらに取り組みを進めています。
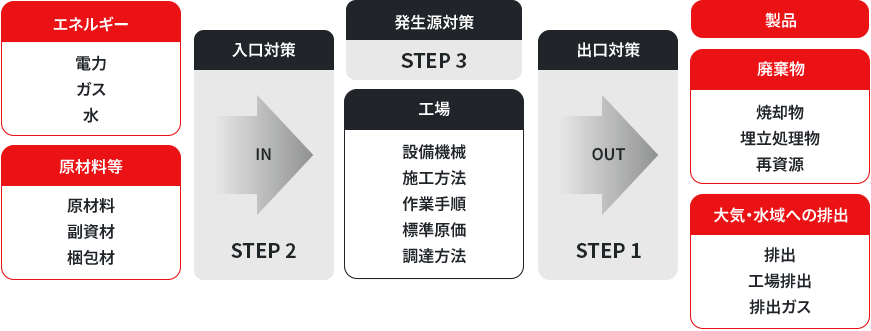
製造時の資源の有効活用・廃棄物削減
切削液の循環利用による廃棄物削減(土岐事業所)
以前は、水溶性切削液を使用しており、臭気やタンク内のヘドロ付着により、半年に1度の割合で切削液の交換を実施する必要がありました。切削液をアルカリイオン水に変更したことで、切削液の腐敗や加工場独特の臭い、加工設備内への汚れの付着を防ぎ、以前より交換周期が延び、廃液発生量を削減することができました。
樹脂パレット、マテハン使用による廃棄物削減(土岐事業所)
鋳物納入時に使用していた木製パレットでの納入を禁止し、繰り返し使用が可能な樹脂パレットやパレティーナによる納入を実現しました。
パレットとパレティーナのすべてにナンバリングをして、納入都度、素材受入担当者立ち会いのもと管理を行っています。
また、板金納入時にも繰り返し使用可能な組立搬送マテハンを使用し、木製パレットやビニールフィルム等の梱包材ゼロ化を達成しました。

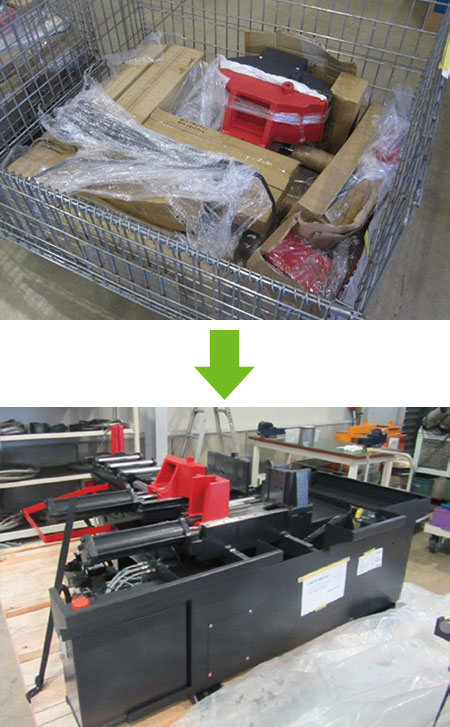
廃材の有効活用(福島工場)
ASR(サイクルローダー=素材集積・供給装置)の廃材をIT-TSU(金型交換装置)のフレームやMARS(自動倉庫)のパレットに有効活用し、廃棄物排出量の削減、新規材料の購入量の削減を図っています。
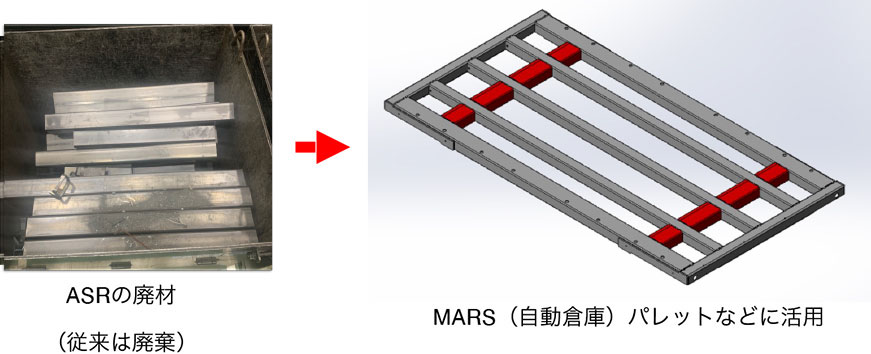
梱包・輸送時の資源の有効活用・廃棄物削減
サプライヤーへの移送や、商品の納入時に使用する梱包材料の廃棄物削減に継続的に取り組んでいます。
従来はプラスチックのエアキャップや油紙、ダンボールなどの梱包材を使用し、開梱後は廃棄していましたが、商品にあわせた専用梱包材を製作し、これを繰り返し使用することで廃棄する梱包材料を減らしています。専用梱包材を使用することによって、梱包・開梱時間の短縮や、梱包の小型化による輸送効率の削減にもつながっています。
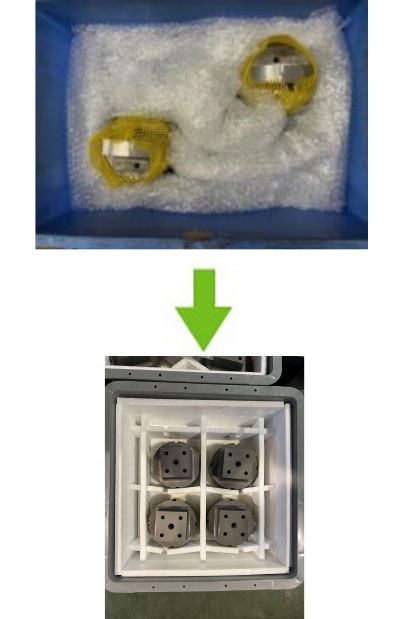
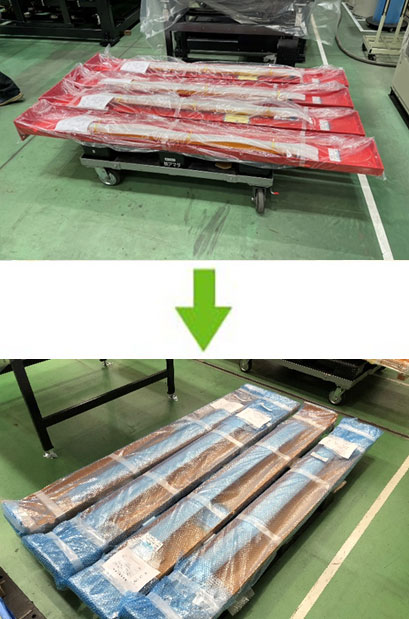
販売時の資源の有効活用・廃棄物削減
商品の販売段階では、アマダエコプロダクツ等の商品の販売活動に加え、展示会における環境配慮にも目を向けています。公共の展示会では使用する装飾部材をリユースが可能なシステム部材に変更して繰り返し利用し、リユースが難しいものはリサイクル処理をしています。
また、自社展示会に使用した装飾部材を伊勢原事業所に搬送し、リユースすることで廃棄物削減に努めています。
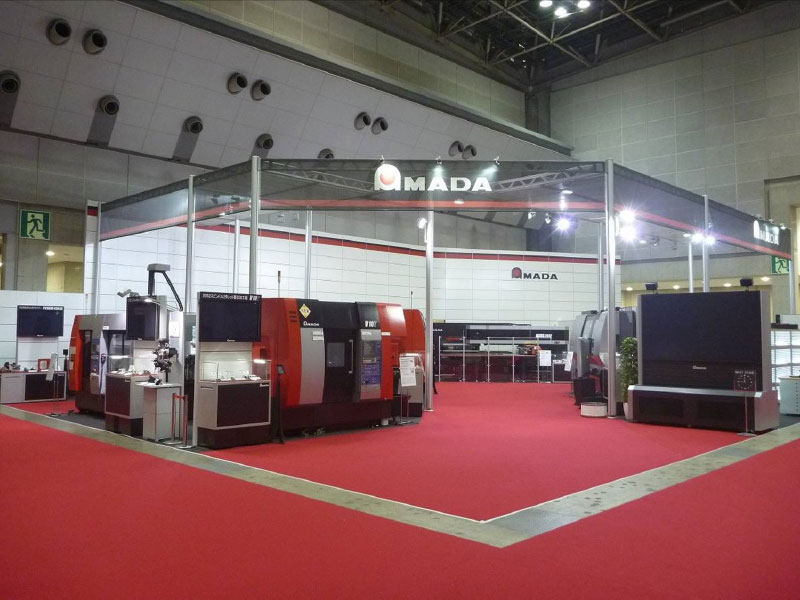
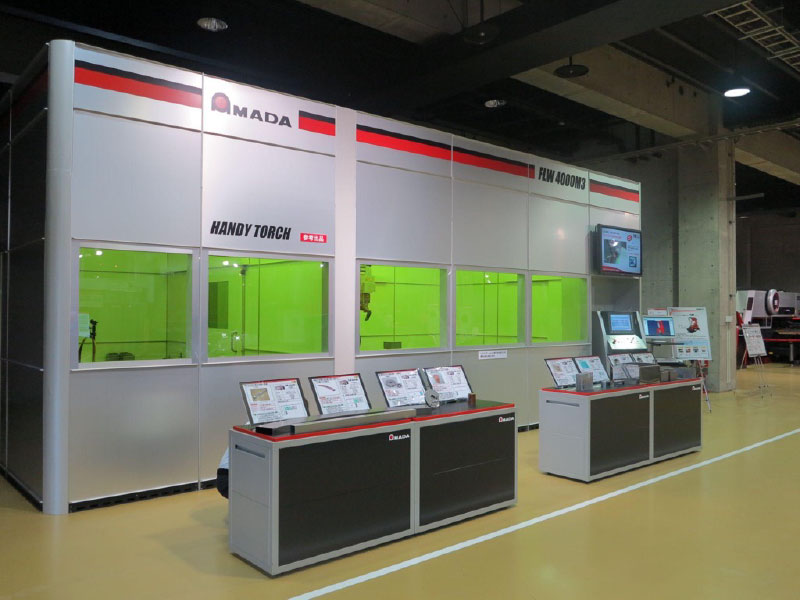
使用済み商品の回収・リサイクル
アマダグループでは商品がその役割を終えて廃棄される際、適切な処理が行われるように、その廃棄業務を委託する企業をアマダグループの選定基準に基づいて認定しています。2008年度から現在まで、パートナー企業2社で全国に5つの認定拠点があり、そのリサイクル工場では各種法令に関するコンプライアンスが確保され、適正処理が実現されています。
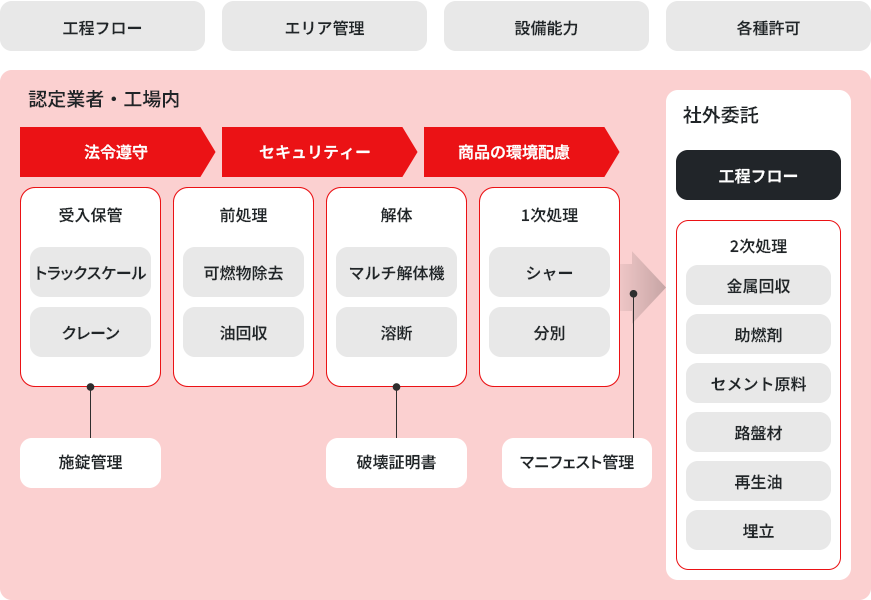
水資源の保全・有効活用
アマダグループ環境方針の「3.自然との共生への取り組み」において、事業活動に伴う自然環境への影響を把握し、水資源の有効活用、生物多様性および生態系の保護を行い自然との共生に取り組むとしています。貴重な水資源の持続可能な利用と保全を目的とし、水リスク評価から実行計画策定を実施し、グループ全体の水使用量を2030年度(2019年度比)までに10%削減することを目標にしています。
グローバルツールによる水リスク評価
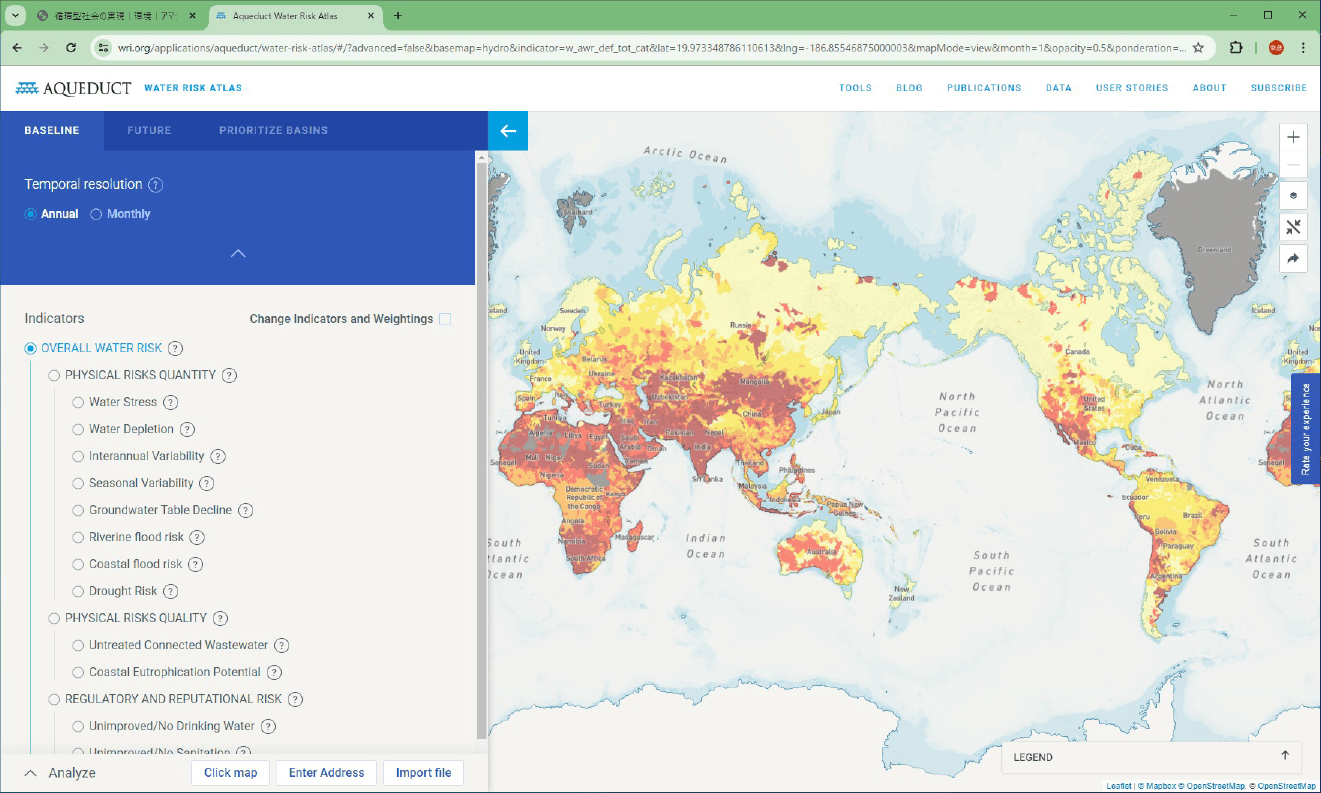
2023年9月にアマダグループの水リスク評価を、世界資源研究所(World Resources Institute)のグローバルツール「Aqueduct」を用いて実施しました。今回は前回までの製造拠点のみの評価から全拠点に対象を拡げて評価しました。国内・海外全66拠点に関わる水リスクを確認・把握しています。
水リスクの総合評価結果では、物理的リスク(量)が高リスクとの結果でした。その中でも高リスクとなる「水ストレスリスク※」レベル4(最高)地域が、16拠点(北米7、欧州3、中国6)であることが分かりました。このアマダグループの水ストレスリスクの高い地域の取水量の合計(49,815㎥)は、海外拠点全体の取水量(133,361㎥)の15.3%を占めています。
- 「水ストレスリスク」とは、水資源量に対する水需要量で計算され、地域の水不足の度合いを示します。
Aqueductで評価可能な12指標
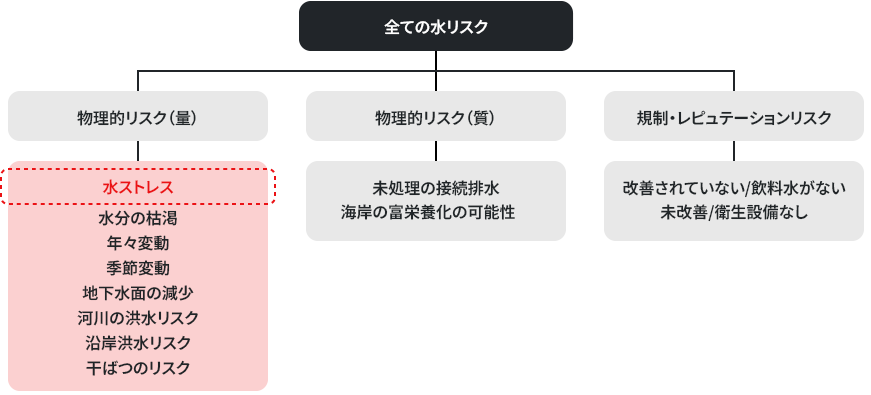
- Aqueduct Water Risk Atlas ホームページをもとに弊社作成
水使用量の削減
海外では灌漑管理や一部設備改善など水利用の効率的な運用による水使用量の削減を行いました(約9,000m³の削減効果)。国内では本社の散水など構内使用の季節ごとに応じたきめ細かな使用量の削減が大きく寄与しました(約22,000m³の削減効果)。その結果、2022年度の実績は2030年までの削減目標(2019年比10%減)を超える成果となりました。実績については下記ページをご覧ください。
環境目標・計画