事業を通じた社会課題解決
アマダグループは、事業を通じて社会に貢献する企業として、社会課題への対応とお客様の要望に応える革新的な商品開発を追求しています。
製造現場でお客様が抱える社会課題をもとに、「4ie」という商品開発コンセプトを策定し、4つの重要なキーワードに基づいて活動しています。
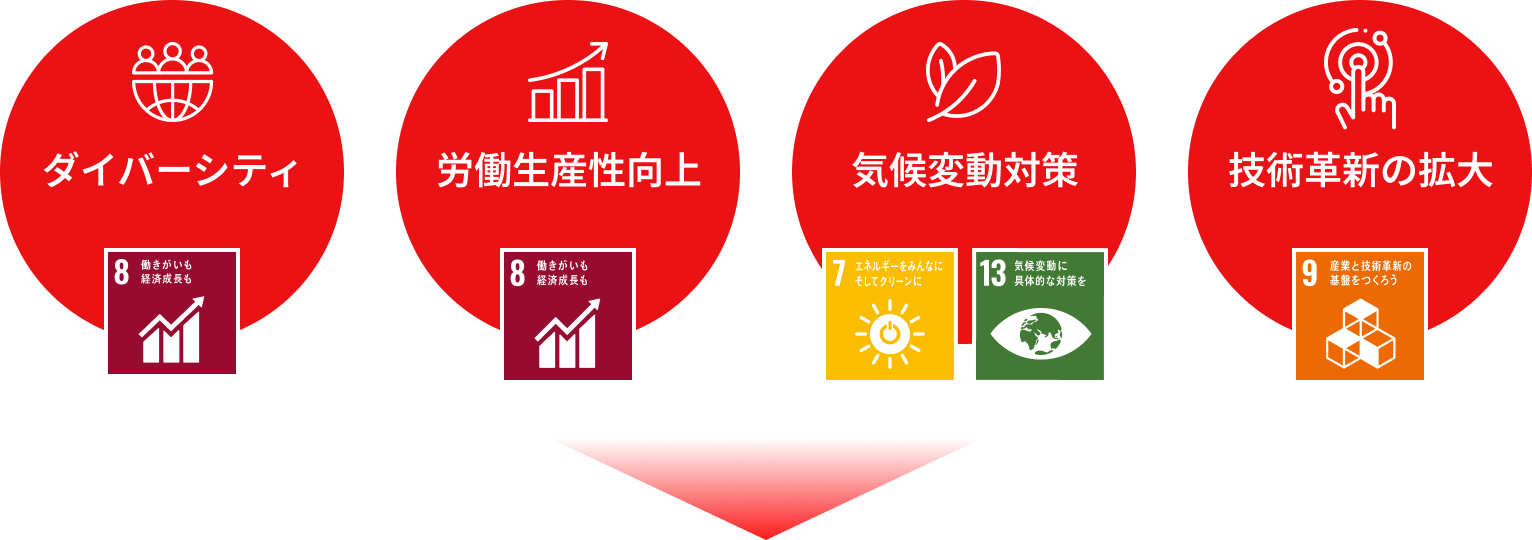
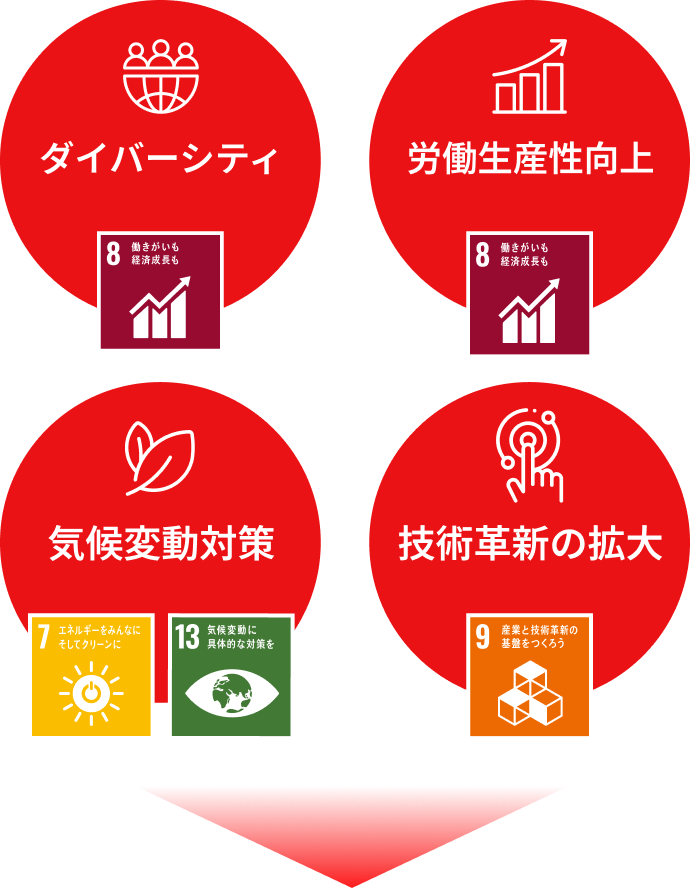
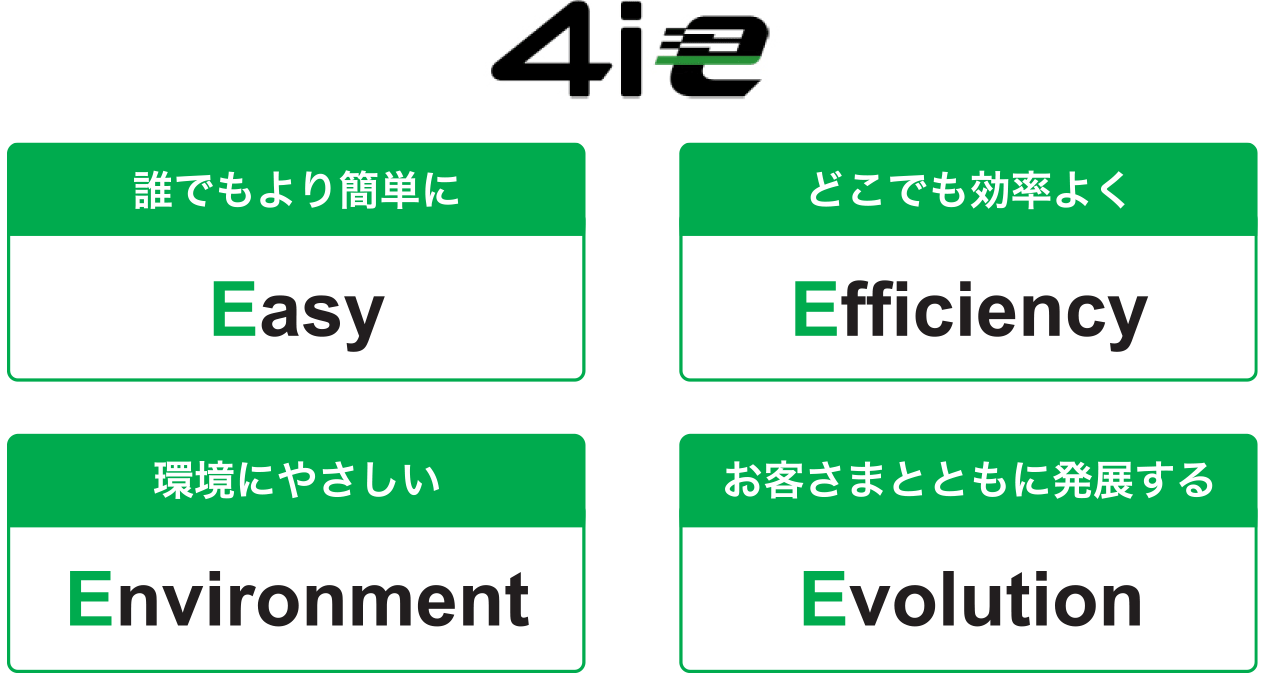
ダイバーシティ
習熟レベルに関わらず、多様な人が効率的かつ安全に作業するためのサポート機能を強化
生産現場では、年齢や性別、国籍などが異なる多様な人材が働くようになっています。しかし、従来の機器は複雑で、スキルや経験に頼る部分も多く、経験の浅いオペレーターにとって、複雑な操作は作業ミスや効率の低下を招いてしまうことがありました。また、教育コストも現場にとって大きな負担でした。
これに対応するため、アマダは操作盤に顔認証用のAIカメラを導入し、オペレーターの言語や習熟レベルに合わせた画面表示を可能にしました。作業に応じてタブレット上にガイダンスが表示され、特殊な形状の加工位置も簡単に設定できるようになりました。さらに、材料供給や金型交換などの重労働で経験を要する作業も自動化を進めています。これらの改善により、経験の少ない作業者でも効率的かつ安全に作業を行うことができるようになりました。
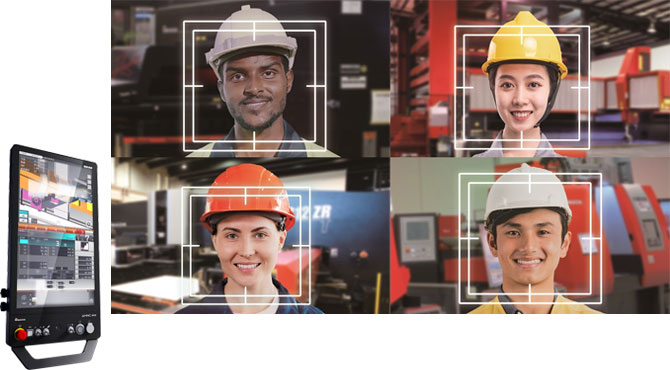
作業者のレベルに合わせた画面表示や言語の切り替えが可能に
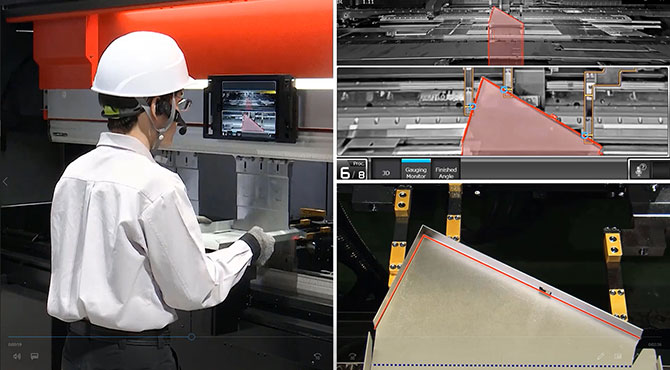
労働生産性向上
リモート確認・操作で複数機器の効率的な運用を実現
世界中で労働生産性の向上とワーク・ライフ・バランスの充実が求められているなか、製造現場では無駄な作業を減らし、マシンの稼働率の向上が目指されています。しかし、機器ごとの操作やそのための動線が多く、マシンに振り回されてしまう現状があり、特に一人の作業者が複数台の機器を受け持つ場合、加工の状況を確認するために頻繁に移動する必要があったり、加工が停止していることに気づかないことが大きなロスになっていました。
これに対応するため、アマダは手持ちのモバイル機器で複数マシンの運転状況をリスト表示するアプリケーションを開発しました。これにより、工場内のどこにいてもマシンの状況を確認できるようになりました。このアプリケーションは加工終了前やアラーム発生時の通知機能、遠隔からの加工スタート、一時停止からの再スタート機能も備えており、より効率的な働き方を支援しています。
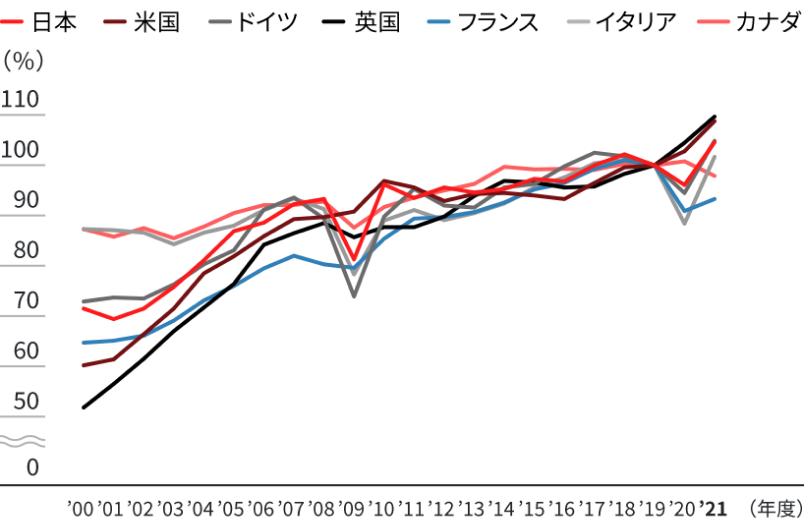
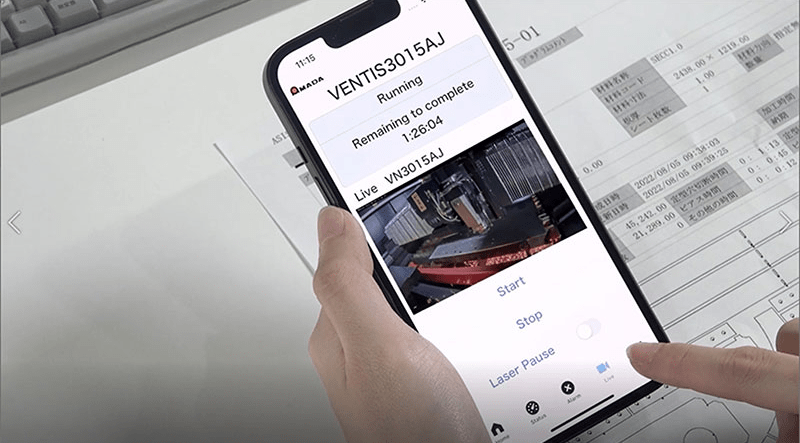
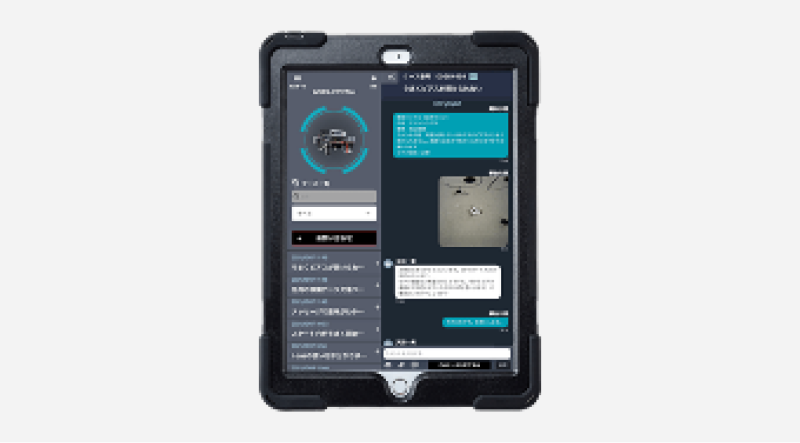
気候変動対策
「見える化」によって、製品の環境負荷の削減をサポート
2021年に開催された国連気候変動枠組条約締約国会議(COP26)において、「2050年までに温室効果ガスの排出実質ゼロ(カーボンニュートラル)を実現する」という大きな目標が掲げられ、各国はその達成に向けて削減目標を設定しています。企業においても、その社会的責任が増大するなか、日々の生産活動における環境への取り組みは、“選ばれる企業”の重要な条件になっています。
これに応えるため、アマダは消費電力量を大幅に削減したエコマシンを開発しました。また、製作した製品のCO₂排出量や、生産活動における環境負荷を「見える化」する機能も開発しており、アマダの基準マシンと比較して、どれだけエコに加工しているかを比較表示することができます。DXソリューション製品と連携することで、製造工程全体のCO₂排出量を集計し、生産管理システムに情報を提供することも可能です。
さらに、中小製造業向けには、企業の温室効果ガス削減目標がパリ協定の目標と整合していることを示す「SBT認証」の取得支援サービスも展開しています。これにより、環境に配慮した持続可能な生産活動を推進しています。
各国の温室効果ガス排出削減目標
日本 | 2030年目標:46%、さらに50%の高みに向けて挑戦 (基準年 2013年度) 長期目標:2050年カーボンニュートラル |
---|---|
米国 | 2030年目標:50~52% (基準年 2005年) 長期目標:2050年カーボンニュートラル |
EU | 2030年目標:55% (基準年 1990年) 長期目標:2050年カーボンニュートラル |
英国 | 2030年目標:68% (基準年 1990年) 長期目標:2050年カーボンニュートラル |
中国 | 2030年目標:GDP当たり65%以上減、絶対量は減少に転じさせる (基準年 2005年) 長期目標:2060年カーボンニュートラル |
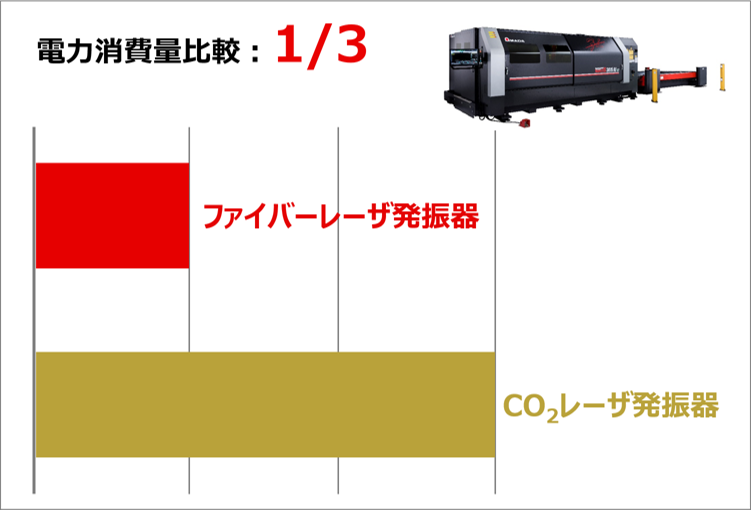
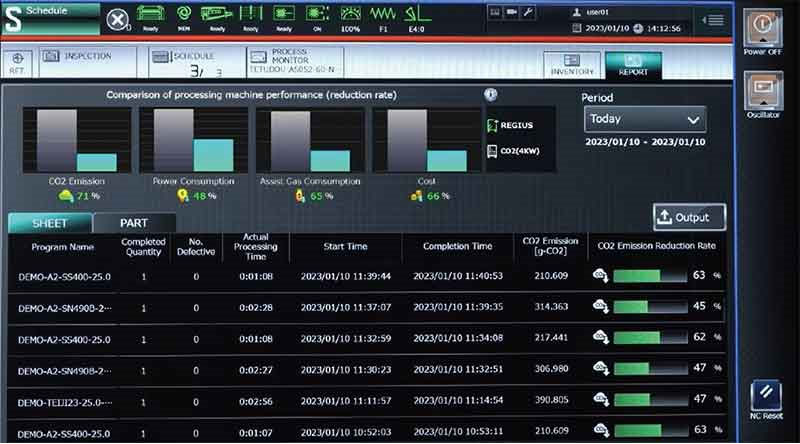
技術革新の拡大
IoTで工場全体をつなぎ、モノづくりをよりスマートに
将来にわたって持続可能で豊かな社会を築くためには、技術革新による産業の改善と発展が不可欠です。アマダは、DX(デジタルトランスフォーメーション)の推進を通じて、この重要な課題に積極的に貢献しています。その一例がスマートファクトリーです。「V-factory」というコンセプトを推進し、マシンを中心に、金型、ソフトウェアなど工場内のあらゆるものをネットワークでつなぎ、IoTサポートセンターとセキュアな通信技術で連携します。これにより、製造の全行程の情報をデジタル化し共有することが可能となり、工場の課題を見える化します。その結果、資源、時間、コストの効率化を実現し、より付加価値の高いモノづくりを推進することができるのです。
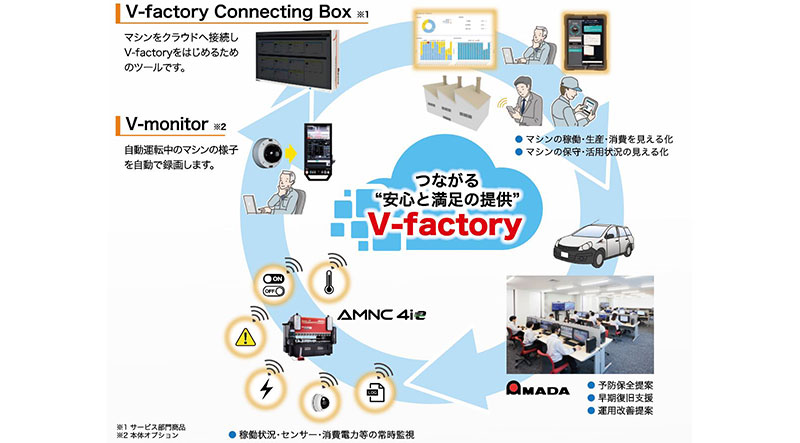
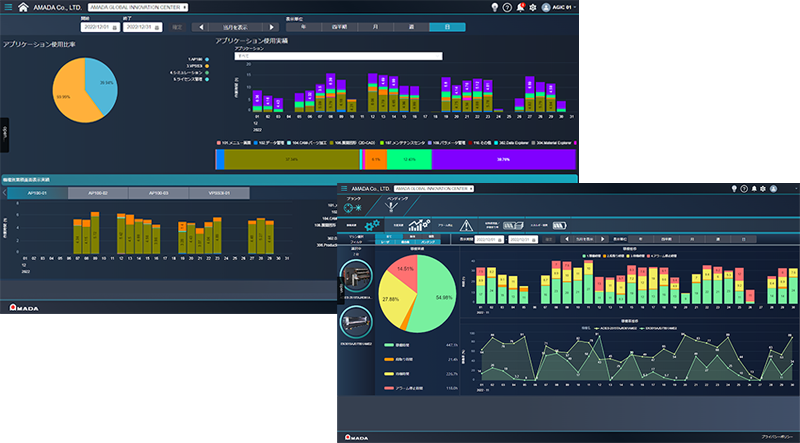