- AE-NT Series
- System Upgrade
- Punching Tooling
- ID-TOGU
- TOGUⅢ
Punching Tooling
NEXⅢ tooling (EM standard)
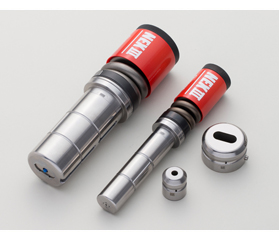
- Digital tool management by ID
- NEX Ⅲ tooling can be disassembled, assembled and adjusted with a single button and without hand tools.
- An optional tool mark-less guide reduces the holddown dents produced on the worksheet surface during punching.
- The punch grinding amount is increased to 6.5 mm for B stations (1-1/4")
Specifications
Tooling type |
Station size |
Spring |
Guide |
Maximum sheet thickness |
Die |
---|---|---|---|---|---|
NCT long / standard |
|
NEX spring ass'y (Unit type) |
Closed guide dedicated to air blow NEX Ⅲ tooling |
SPC:6.35 |
Vacuum die |
Contouring tool (EM standard)
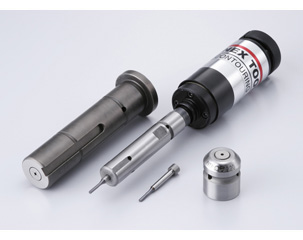
Precision nibbling on 0.5 mm centers allows for special processing without dedicated tooling. Various measures are employed to accommodate high hit rates.
Specifications
Tooling type |
Station size |
Diameter of punch tip |
Die/Applicable die |
Maximum Sheet thickness |
Material |
---|---|---|---|---|---|
NCT long Air-blow type |
φ2.0 |
Power vacuum type / Die bush type |
SPC:1.6 |
Punch tip: APH |
Slotting tool III (EM standard)
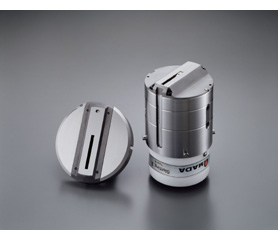
Joint mark-less processing is possible until the repositioning of the clamps.
Specifications
Tooling type |
Station size |
Cut width (mm) |
Maximum sheet thickness |
Maximum sheet thickness |
Maximum feed pitch |
---|---|---|---|---|---|
Slotting tool III |
3 |
6~10 |
SPCC:2.3 |
SPCC:2.3 |
1.6t<t→20 |
4 |
1.6t<t→30 |
Inch bend tooling (EM standard)
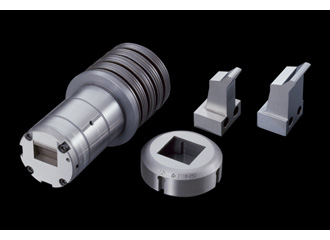
Small flange bending is dangerous to perform on the press brake but can be safely done on the turret punch press.
Four different thicknesses can be handled simply by changing the direction of the die.
Specifications
Tooling type |
Station size |
Bend direction |
Bend accuracy |
Sheet thickness/ die 4 sides |
Punch tip size |
---|---|---|---|---|---|
Inch bend |
2 |
Downward forming |
±30' |
0.5 |
10/15/20/25/30 |
Work chute tooling (EM standard)
High-speed microjoint breaking tool for final cutting and part ejection.
Manual microjoint breaking is now automated on the turret punch press.
Specifications
Tooling type |
Station size |
Maximum work size (mm) |
---|---|---|
Work chute tooling |
3 |
65 square |
4 |
85 square |
MPT tapping tools
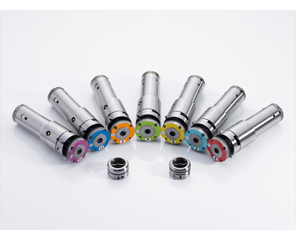
Tapping (with both thread cutting and forming taps) can be performed on the turret punch press.
Specifications
Tooling type |
Station size |
Type of tap |
Size of tap |
Maximum sheet thickness |
Tapping time |
---|---|---|---|---|---|
MPT tapping unit |
1 |
Thread cutting taps and forming taps |
M2.5, M2.6, M3, M4, M5, M6, M8 |
SPC:6.0 |
2 |
Chamfering tool (EM standard)
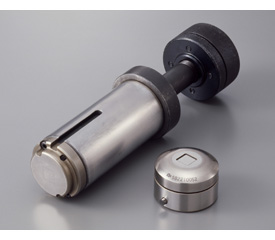
Tool shapes are created to suit part shapes.
Bottom burrs are coiled back into the part on the turret punch press to reduce the deburring time.
Specifications
Tooling type |
Station size |
Chamfering value |
Sheet |
Sheet thickness |
Processing direction |
---|---|---|---|---|---|
NCT long |
|
approx. C 0.2 |
SPC/AL/SUS |
over 0.5 |
upward |
High speed marking tool (EM standard)
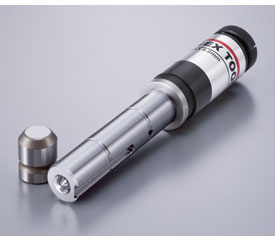
Sorting of parts, formerly done manually.
High-speed marking on both the top and bottom surfaces of workpieces helps to reduce secondary operations.
Standard tooling
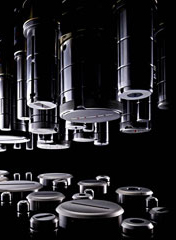
AMADA's standard turret punch press tooling allows for high-quality processing.
Special order tooling
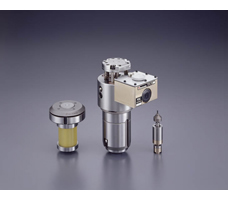
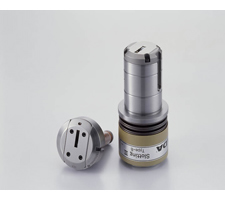
AMADA's forming tools provide for high-quality processing of sheet reinforcements and part mounting bases, and for high-quality forming of grills and various other shapes.
Special tools are also made to the specifications of customers.
*For Japan domestic market.
For any inquires, please contact local AMADA branch office.
Punching Machines Top|EM-ZR Series|EM-MⅡ Series|LS-2612E|AE-NT Series
System Upgrade|Punching Tooling|ID-TOGU|TOGUⅢ