Conventional production methods are simply insufficient for satisfying the need for single-form product without weld structures at low cost. Canvassing for appropriate methods, we received a recommendation to "strike and stretch". Although we decided to run with this simple and clear-cut suggestion, it was no easy matter to devise a practical means and we took a long, hard look at the processes involved.
In the end, we settled on four processes: 1) Unfolded to a semicircular material and perforations with a turret punch press, 2) R-bend by brake roller, 3) Feed-rolling and 4) Cutting and finishing. In the rolling process, we used the unprecedented method of uniform rolling 1,300 times at a pitch of 0.5mm to obtain a distance of 650 mm to the tip. We adopted several other refinements and worked our way to completion.The result was a transformation of conceptualization. We were able to achieve structural harmony by using processing methods that held scratches to a minimum on the specular material susceptible to scratches. We suppose this was a major factor in this award. Craftsmanship requires more than just equipment. We plan to continue to incorporate new ideas into our work
|
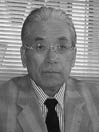
Minoru Ishikawa
President
|